近年来,随着相关政策的逐步落实,储能赛道市场规模持续扩大,呈现出蓬勃发展的趋势。中国物理与化学电源行业协会储能应用分会预计,到2025年,新型储能产业规模有望突破万亿,到2030年预计接近3万亿。
高增长机遇之下,储能行业内的“厮杀”也愈发激烈,“行业内卷”和“产能过剩”等情况屡见不鲜,业内投标、中标价格不断创下新低,一众系统集成企业面临盈利压力,储能市场“增收不增利”问题日益突出。
受储能全产业链降本高压影响,实现极致降本成为行业企业保持竞争优势的迫切需求。
另一方面,在市场规模持续扩大的同时,储能线生产流程也逐渐显露出一系列痛点和难点,直接影响着储能行业的生产效率、产能以及企业的生产成本,具体表现在:
储能线生产流程中,大量的人工周转环节成为一大制约因素。从原材料的搬运到成品的包装,过程中充斥着繁琐而低效的人工操作。这不仅降低了生产效率,还增加了生产周期,制约了储能行业应对市场需求的速度。
储能线的生产工序衔接度不足,导致柔性化生产能力不足。生产线之间的信息传递不畅,导致生产计划的不灵活,无法迅速应对市场的变化。这使得企业在面对定制化需求或市场突发事件时显得力不从心。
某储能柜装配线甚至出现了“人工蹬踹协助电池包入柜”的粗放式作业,自动化程度不足问题突出。自动化技术的缺失不仅影响生产效率,还增加了生产过程中的不确定性和安全隐患,制约了产能的提升空间。
上述情况产生的低效率、生产衔接度低、自动化程度不足等问题,导致储能企业不得不面对生产成本居高不下的困扰,这也会进一步对储能产品的竞争力产生直接影响,波及至整个储能行业的可持续发展。

为应对诸多行业痛点,磅旗科技围绕储能工序,创新推出了储能行业的从电芯到装配全流程的数字化少人化的降本增效方案。该方案旨在全方位提升生产效能并实现极致降本,以全场景全流程数字中台LDS为核心,紧紧聚焦于降本增效目标,通过打通物流和生产侧的设备和系统数据链,大大减少工作作业工序、为整个储能生产流程提供数字化、少人化、智能化的解决方案。
在某头部企业的储能电芯涂布、辊分、模切、卷绕等生产环节中,传统的上下料和辅料配送方式存在,单拉线工位上下料、上下工序衔接还是依靠大量人工操作、效率低下的问题,影响了整体生产效率和单位制造成本。 引入磅旗的储能行业物流无人化解决方案,将生产线上的上下料工位上下工序的链接进行数字化、无人化改造,实现全线数字化无人化管理,实现自动叫料、物料智能拉动、任务智能分配与调度管理,实现快速、准确的电芯产线物料运输。
通过引入磅旗的储能电芯段解决方案,降本增效效果显著。每条拉线减少OPN作业人员5人,整体生产线作业减员50%,生产响应速度提高了35%,成功减少了人为操作引起的误差和延误。
当前,行业电池组的大部分是人工装配模式,甚至某些企业储能柜装配线出现了“人工蹬踹电池包入柜”的粗放式作业,不仅费人、而且效率低、生产安全隐患大。
为应对储能制造装配的多重挑战,磅旗提供了多种集装箱装配方式,包括重载AGV、板链式和轨道式等。这些创新的集装箱装配方式共同构建了储能柜装配数字化车间线体解决方案,实现了集装箱上/下线、PACK簇安装自动化等智能功能。
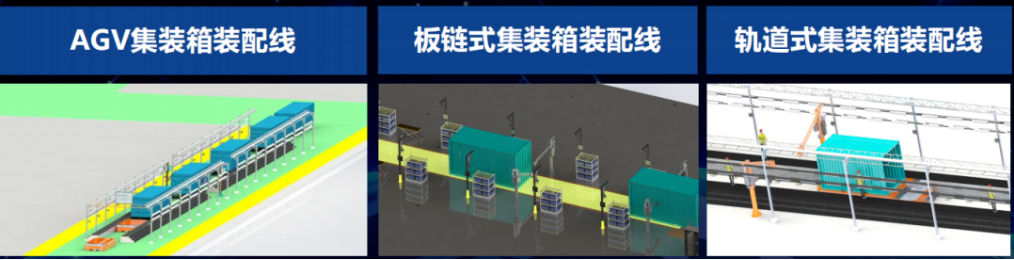
该客户的储能集装箱存在电池组搬运与装配困难、装配作业空间局限等问题,特别是模组重、入柜难,效率低,而且生产安全隐患大。
为解决客户痛点,磅旗采用板链式输送方式,构建车间线体数字化解决方案。通过自动牵引系统,实现集装箱在装配车间内的智能运输,减轻了人工搬运的负担。 同时,该企业还通过磅旗提供的自动化装配系统实现了PACK簇的自动安装,通过机器人和自动化设备完成电池组件的精准组装,提高了装配的准确性和效率。 通过磅旗的储能解决方案,该企业客户成功降低了储能集装箱装配人力投入的40%,提高了装配效率和生产线的整体产能;集装箱装配方式减少了作业空间的限制,提高了生产线的灵活性和布局效率;自动化装配系统提高了准确性,装配过程中的误差率降低了75%,极大提升了产品质量。
综合而言,磅旗科技储能行业物流侧数字化无人化解决方案无疑是储能行业的一大降本利器,通过数字化、自动化和无人化技术,磅旗不仅为企业客户提供了可持续的降本增效方案,助力其在激烈竞争中脱颖而出,更推动了整个储能行业的降本增效和产业协同再上新台阶。